MFL - Magnetic Flow Leaks
Magnetic Flow Leak Inspection (MFL) is a non-destructive testing (NDT) method used to detect and evaluate corrosion, pitting, and wall loss in metal storage tanks and pipes. A powerful magnet is used to magnetize steel. In areas where there is corrosion or lack of metal, the magnetic field "filters" the steel. MFL tools use sensors placed between the magnet poles to identify the leak field.
In tank floor inspection, the tank floor is swept with the MFL tool. The area is flooded with magnetic flux and earth magnets are used to temporarily magnetize steel while recording and analyzing changes in the magnetic field. If the magnetic field is distorted, there are internal or external defects, such as pitting or corrosion, and this distortion or "leakage" can be measured by the sensors. Technicians proceed to mark areas that need to be verified by visual inspections and ultrasound. The results obtained from the MFL inspection can be reported and used to establish an existing baseline for the equipment or to determine the remaining wall corrosion and fitness calculations for the service in accordance with API 653, EEMUA and other applicable standards.
Instead of replacing plant assets, MFL condition assessment and point repair can often extend the life of a storage tank or pipe. MFL inspection technology enables asset managers to proactively manage a tank or pipe by repairing problematic locations. MFL inspection reduces the risk of tank or pipe failure.
At ISS RD, SRL we have experienced inspectors with extensive knowledge the application of the MFL technique for tank and pipe floors. We use equipment such as the MFE Mark 2 as part of tank inspections under API 653 and pipes under API 570.

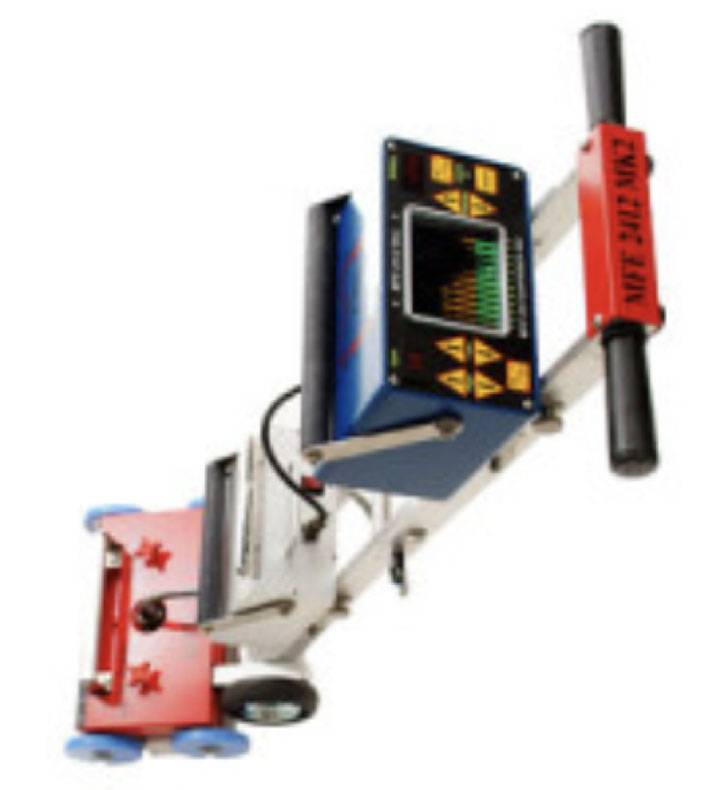